Extending the life of your ion exchange resin in boiler feed water applications
Did you know that when producing steam, it is most effectively accomplished by utilizing a decarbonation process? Decarbonation and Degasification is the most economical way to process fluent water pre-Ion exchange treatment through a vertically packed tower called a decarbonator, often called a degasifier. This is the most economical method to remove carbon dioxide (CO2) and Hydrogen Sulfide (H2S) to prevent the formation of carbonic acid. Other corrosive conditions are Degasification and Decarbonation, which will extend the life of the ion exchange resin. If CO2 levels remain high in the inlet feed water to the ion exchange system, the resin beds, whether cation or anion, will require more frequent regeneration, and your chemical usage and cost will rise.
In industrial applications, it’s easy to overlook.
Often, there is insufficient focus on selecting the right decarbonation or degasification system to ensure that the process water treatment system performs at the highest optimal level. For water filtration, when the primary process is membrane filtration, often referred to as “reverse osmosis, " too little attention is given to properly removing CO2 from the process to lower the pH and adjust the alkalinity.
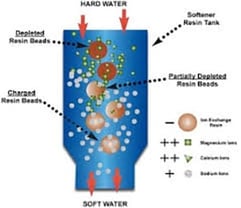
A high level of CO2 and acidic pH will increase the consumption of ion exchange resins before injecting into a boiler feed process to produce steam. Degasification towers are available in several configurations, some utilize steam, and some work without steam injection. Steam injection is often required when removing dissolved oxygen (DO) in the water is needed. When there is no need to remove DO, a normally forced draft degasification tower is much more economical to purchase and operate and frees up valuable steam to be applied in other industrial operations.
Chemical operating costs for industrial water applications can be very high!
The consumption of amine for the regeneration of resins will drastically increase if the water process is not properly adjusted and the carbon dioxide (CO2) is not removed before the ion exchange water softening process. This mistake can also add to ion exchange failure and an increased water hardness level resulting in scaling and corrosion inside the boiler tubes. If the boiler tubes scale or a buildup of corrosion occurs inside the tubes, the system's efficiency is reduced, and steam production falls. If left untreated for a long period, the complete boiler feed system may fail and require costly replacement. You must always consult your decarbonation/degasification manufacturer to optimize the removal of CO2 and maintain the pH balance to avoid unnecessary boiler damage.
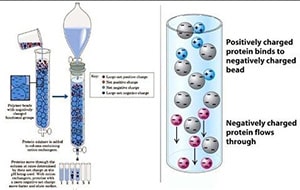
You must always remember it is very important to select and properly size the Degasification tower or Decarbonation tower with the proper “distribution” system to maximize the removal of entrained gases and reduce and or eliminate harmful corrosive conditions that can and will damage your steam production system components like your boiler and heat exchangers. If the critical equipment is inside of a building or near the degasification process, you should also consider utilizing a chemical scrubber or biological scrubber to prevent corrosive and harmful gases from collecting on or around the systems and in the presence of the operators to learn more about this by visiting Industrial Water Treatment. For more information or to learn more, contact the professionals at DeLoach Industries Inc. at (941) 371-4995.