Water purification is critical in industrial operations, especially when it comes to removing dissolved gases that can cause corrosion and compromise the efficiency of equipment. Various methods exist to address these issues, with Forced Draft Degasification (FDD) systems often cited as one of the best options. However, while FDD systems have clear advantages, they may not always be the ideal solution depending on specific needs. In this article, we'll explore the ins and outs of Forced Draft Degasification, weigh its benefits and drawbacks, and compare it to alternative methods to help you determine if it's truly the best choice for your water purification needs.
Understanding Forced Draft Degasification Systems
Forced Draft Degasification systems are designed to remove dissolved gases, such as carbon dioxide (CO2) and hydrogen sulfide (H2S), from water, which can cause significant problems in industrial equipment. The principle behind FDD is simple but effective: water flows through a vertically structured tower, typically packed with media that maximizes the surface area. As water travels downward, a cross-current of air is forced through the system, helping to strip out unwanted gases.
This interaction between air and water allows for the efficient removal of these gases, which otherwise would contribute to the deterioration of industrial equipment through corrosion. Corrosive environments not only shorten the lifespan of machinery but also increase maintenance costs, leading to inefficiencies that can disrupt entire operations. The goal of FDD systems is to mitigate these risks, making water safe for industrial use and protecting expensive equipment investments.
These systems are widely used in industries such as power generation, chemical processing, and oil refining, where the presence of dissolved gases can lead to substantial equipment failure or process inefficiencies. The vertical design of the FDD system enables it to handle large volumes of water efficiently, making it ideal for high-capacity industrial needs. The simplicity of the FDD system, combined with its ability to consistently remove dissolved gases, makes it a preferred choice for many industrial operations that prioritize reliability and cost-effectiveness in their water treatment systems.
Read More
Topics:
hydrogen sulfide (H2S),
carbon dioxide,
degasifier,
Deagasification,
DeLoach Industries, Inc.,
Forced Draft,
Industrial water treatment
Clean water is essential for sustaining life, and ensuring its purity is a priority for environmental agencies worldwide. However, a growing concern has emerged in recent years – the presence of perfluoroalkyl and polyfluoroalkyl substances (PFAS) in drinking water. PFAS are persistent, human-made chemicals widely used in various industrial and consumer products, posing a significant threat to water sources and public health. Here, we'll explore the strategies and challenges involved in removing PFAS from drinking water, shedding light on the ongoing efforts by environmental agencies to manage and dispose of these persistent chemicals.
Understanding PFAS Contamination
PFAS contamination is a complex issue stemming from the widespread use of these chemicals in industries such as manufacturing, firefighting, and even everyday household products. These substances are known for their heat, water, and oil resistance, making them valuable for various applications. However, their persistence in the environment has raised serious concerns.
PFAS enter water sources through various pathways, including industrial discharges, wastewater treatment plants, and the use of firefighting foams. Once in the water, PFAS can accumulate over time, threatening aquatic ecosystems and, ultimately, human health. Long-term exposure to PFAS has been linked to adverse health effects, including developmental issues, immune system suppression, and an increased risk of certain cancers.
Strategies for Removing PFAS from Drinking Water
Addressing PFAS contamination requires a multifaceted approach, combining advanced water treatment technologies with comprehensive regulatory measures. Several strategies have been employed to remove PFAS from drinking water, each with its challenges.
Activated Carbon Filtration
One widely adopted method for PFAS removal is activated carbon filtration. Activated carbon has a high affinity for PFAS compounds, effectively adsorbing them from the water. However, the efficiency of this method can be influenced by factors such as the type of activated carbon used, the water's chemical composition, and the presence of other contaminants. Additionally, the disposal of used activated carbon loaded with PFAS poses a significant challenge, as it can contribute to environmental contamination if not handled properly.
Ion Exchange Resins
Ion exchange resins are another technology employed to remove PFAS from drinking water. These resins replace PFAS ions with less harmful ions, effectively capturing and removing them from the water. While ion exchange can be highly effective, managing the used resins saturated with PFAS is challenging. Proper disposal methods must be implemented to prevent the release of these persistent chemicals back into the environment.
Advanced Oxidation Processes (AOPs)
Advanced Oxidation Processes (AOPs) involve using powerful oxidants to break down PFAS compounds into non-toxic byproducts. Techniques such as ozonation, ultraviolet (UV) irradiation, and hydrogen peroxide treatment fall under AOPs. While these methods show promise in PFAS degradation, they can be energy-intensive and may produce secondary pollutants. Balancing effectiveness with environmental impact remains a key challenge in implementing AOPs for large-scale water treatment.
Read More
Topics:
water quality,
water treatment,
advanced treatment solutions,
Safe drinking water,
DeLoach Industries, Inc.,
Ion exchange,
Drinking Water,
DeLoach Industries,
removing PFAS & PFOS,
pfas exposure,
health effects of pfas,
exposure to pfas,
water treatment standards,
PFOS,
water purification systems,
RO process for PFAS removal,
Remove PFAS,
AOPs,
Water Treatment Technologies,
Perfluoroalkyl Substances,
Advanced Oxidation Processes,
Polyfluoroalkyl Substances
Clean and safe water is a fundamental requirement for our well-being, yet the increasing presence of PFAS contaminants in industrial water sources remains a significant cause for alarm.
In this blog, we’ll delve into the pressing issue of PFAS contamination in industrial water supplies and shed light on how Reverse Osmosis (RO) technology is a robust safeguard against this concern. We will not only explore the effectiveness of RO in eliminating PFAS but also the distinct advantages it offers over conventional water treatment methods.
The Growing Concern of PFAS in Industrial Water
Per- and Polyfluoroalkyl Substances (PFAS) have become a growing concern in industrial water sources. Synthetic chemicals like PFOA and PFOS can stay in the environment and build up, causing significant risks to people and the ecosystem.
Read More
Topics:
water quality,
water treatment,
advanced treatment solutions,
Safe drinking water,
municipal water systems,
DeLoach Industries, Inc.,
Drinking Water,
DeLoach Industries,
removing PFAS & PFOS,
pfas exposure,
health effects of pfas,
exposure to pfas,
water treatment standards,
PFOS,
water purification systems
I will explore the potential risks of exposure to two members of a family of man-made chemicals called PFAS.
These chemicals are PFOA and PFOS, "poly-fluoroalkyl substances."
I will discuss the sources of PFOA and PFOS. These include leaching from industrial sites, the use of consumer products, and food and water contamination.
I will also discuss the exposure pathways of PFOA and PFOS. I will examine the regulations and guidelines for the use of these chemicals. I will also investigate their impact on the environment and various industries.
I will guide long-term human health effects.
This guide covers the potential risks of pfo's and pfoa's. It explains their sources and exposure pathways. It also looks at regulations and guidelines for their usage and impact on the environment and industries.
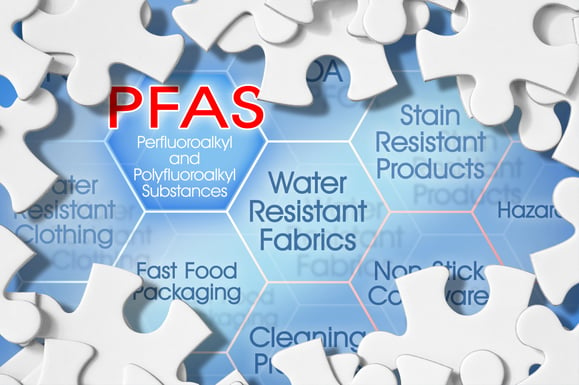
Introduction to PFOA and PFOS
Read More
Topics:
water treatment issues,
water quality,
water treatment,
advanced treatment solutions,
FDA,
Safe drinking water,
wastewater,
Global,
RO system,
DeLoach Industries, Inc.,
Drinking Water,
PFA's,
DeLoach Industries,
Cosmetics,
make-up,
water process system,
removing PFAS & PFOS,
pfas exposure,
health effects of pfas,
nonstick cookware,
wastewater treatment system,
water treatment standards,
PFOS,
safe drinking water act,
pfoa regulations,
the environmental protection agency,
drinking water standards,
adverse health effects,
water resistant clothing,
environmental safety
If you’ve been following the news, you know a growing problem with PFAS (per- and poly-fluoroalkyl substances) exists.
PFAS, a group of synthetic chemicals in a wide range of products, is causing a growing concern. Despite their widespread use, some PFAS compounds have been found to degrade into potentially harmful byproducts like PFAS-methyl tetrahydrofuran. What's more alarming is that these chemicals have infiltrated our drinking water sources, even in areas with high water tables. This is why it's crucial to understand effective methods for removing PFAS from water. What should you do if you suspect that there’s a problem with your water? Check the source of the water, test it, and treat it if necessary.
Follow these steps to remove PFAS from drinking water.
Test Your Water
Although knowing how to remove contaminants is essential, it’s even more important to understand how to test your water for contamination. A water test kit can help you determine whether there are contaminants in your water and whether they are at a dangerous level. You can purchase water test kits at grocery stores, hardware stores, and online retailers. Generally, these kits come with the standard set of tests for a home water filtration system, but they also often include tests for specific contaminants. Use these tests to determine whether your water is safe to drink. If your water contains contaminants, remove them from your water source. This can be done by digging a more bottomless well, installing a water filtration system, or getting a water purification system. If your water does not contain contaminants, you don’t need to do anything except continue drinking your water.
Check the Source
Understanding the source of your water is a crucial step in addressing contamination. Whether you have a well or a water treatment system, knowing where your water comes from can provide valuable insights. By tracing the water's journey from the source, you can determine if contamination occurs upstream. This knowledge is essential for well owners, who might overlook the significance of understanding their water source. If you find contamination at the source, you can address it immediately, such as reducing the distance between the source and your dwelling or seeking alternative, uncontaminated sources.
Read More
Topics:
water treatment issues,
water quality,
odor control,
water treatment,
advanced treatment solutions,
Chemical Odor,
Safe drinking water,
RO system,
filters,
Filter Media,
residential well water systems,
DeLoach Industries, Inc.,
backwash,
Carbon Filter,
Micron Filter,
Drinking Water,
Clean Water,
Contaminated Water,
Water Source,
Sediment Filter,
PFA's,
Water Test,
Water Test Kit
Water is essential for life, but not all water is safe to drink.
Contaminants like perfluorooctanoic acid (PFOA) and perfluorooctanesulfonic acid (PFOS), collectively known as PFAS, have been a growing concern in our water supply. Fortunately, there's a remarkable solution that often goes unnoticed: carbon absorption filters. Here, we'll explore the technology behind carbon absorption filters, how they effectively trap PFAS and their numerous benefits in water treatment.
Understanding Carbon Absorption Technology
Before delving into how carbon filters combat PFAS, let’s review the fundamentals of carbon absorption technology. Activated carbon, the hero in this story, is an incredibly porous material with a vast surface area, typically derived from sources like coconut shells, wood, or coal. This porous structure is what makes activated carbon ideal for trapping contaminants.
1. Activated Carbon's Structure: Think of activated carbon like a sponge, but not just any ordinary sponge – it's a super sponge! At a microscopic level, it's filled with tiny pores and holes, creating a vast and intricate network. Imagine walking through a maze with endless twists and turns – that's what the structure of activated carbon looks like. And why does this matter? Because all those nooks and crannies provide a massive surface area. It's like having a big, open field instead of a cramped room. This extra space is perfect for grabbing onto molecules, kind of like how Velcro sticks to fabric. This process is called adsorption, where molecules stick to the surface of the carbon rather than getting soaked up inside like a regular sponge.
2. Adsorption vs. Absorption: Let's clear up some confusion between two similar-sounding words. Absorption is like when a sponge soaks up water – it goes inside the sponge. But adsorption is different; it's all about what happens on the surface. Imagine you're playing with magnets. When they attract and stick together, that's like adsorption. Activated carbon is a magnet for contaminants. It doesn't suck them in like a vacuum; instead, it attracts them and sticks them onto its surface, where they stay put. So, while absorption is about taking things in, adsorption is about grabbing onto things on the outside.
3. Adsorbent Specificity: One of the remarkable features of activated carbon is its remarkable versatility and ability to adsorb a wide range of contaminants, including volatile organic compounds (VOCs), which are harmful chemicals emitted from products like paints and cleaning supplies, chlorine, commonly found in water disinfection processes, and, most importantly, PFAS, notorious for their widespread presence in water sources and resistance to degradation, making activated carbon an indispensable tool in combating environmental pollution.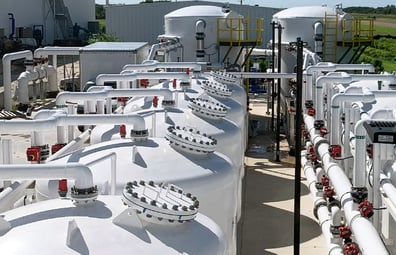
Read More
Topics:
water quality,
water treatment,
advanced treatment solutions,
Safe drinking water,
municipal water systems,
DeLoach Industries, Inc.,
Drinking Water,
DeLoach Industries,
carbon filters,
removing PFAS & PFOS,
pfas exposure,
health effects of pfas,
exposure to pfas,
water treatment standards,
PFOS,
drinking water standards,
forever chemicals,
water purification systems,
carbon absorption
In recent years, PFOA and PFOS, commonly known as "forever chemicals," have raised concerns among municipalities, food and beverage industries, and commercial facilities in the USA and around the globe. These synthetic chemicals, which never break down and pose significant health risks, have been detected in water, food supplies, and even bottled purified water. As new EPA regulations take effect in 2024, industries are searching for effective and cost-efficient methods to remove these hazardous substances from their water supply. Fortunately, advanced water purification technologies such as microfiltration, ultrafiltration, and reverse osmosis can address these challenges.
Read More
Topics:
water quality,
advanced treatment solutions,
Safe drinking water,
RO system,
municipal water systems,
DeLoach Industries, Inc.,
Drinking Water,
DeLoach Industries,
reverse osmosis,
water process system,
removing PFAS & PFOS,
pfas exposure,
health effects of pfas,
exposure to pfas,
water treatment standards,
PFOS,
safe drinking water act,
the environmental protection agency,
drinking water standards,
forever chemicals,
water purification systems,
microfiltration and ultrafiltration,
potable water,
membrane technology,
types of membranes,
flat sheet,
spirally wound
Computer-aided design systems and the advancements in water treatment solutions.
These unique cad design tools have allowed our society to progress rapidly. There have been drastic improvements within the CAD world. CAD computer-aided design programs became commercially available in 1964 when large companies like IBM, GM, and Lockheed Martin began leveraging computerized graphical display systems. These foundational programs are still the basis for some of the most widely used programs.
To this day, 2D CAD is used regularly throughout multiple industries, including Water Treatment, Municipal, Food & Beverage, Commercial, and Pisciculture. While 3D CAD has many advantages over traditional 2D, it is essential to consider your product and its end user. All fabrication drawings, from structural to electrical, are read on 2D paper.
Architects and civil engineers use 2D to convey their ideas to cities, companies, and private parties. Electrical engineers create complex wiring diagrams in 2D only. Due to the clarity provided and adhering to standards followed worldwide.
Figure: Example of a 2D CAD Drawing.
On the other hand, the 3D CAD design program is a young technology that has provided amazing breakthroughs in workflow increases and cost savings. 3D modeling became widely accessible in the late 1980s. It became a challenge that required engineers to rewire their brains to create models in the third dimension. 3D CAD software has two main categories:
- Parametric modeling
- Direct modeling
Direct modeling: grants the user flexibility by allowing them to define and capture geometry quickly without concentrating on dimensions. Direct modeling is perfect for prototyping, considering how agile the method is. A simple analogy would be to imagine working with modeling clay. Rather than measuring, you push and pull until you are satisfied with the geometry.
Read More
Topics:
design intent,
2D CAD Drawing,
3D CAD Software,
3d modeling,
computer-aided design,
parametric cad,
type of modeling,
parametric modeling
PFOA and PFOS are man-made chemicals used in various products to simplify life.
Forever chemicals, also known as synthetic chemicals called PFAS, have gained recognition. Scientists created these chemicals to make products resistant to water, stains, and sticking. The United States initially utilized them in the 1950s.
DuPont introduced Teflon in the 1950s to help Americans have nonstick cookware and make their lives easier. Americans and people from other countries liked this new improvement and soon used these substances in many different products.
These chemicals are resistant to water and lipids, so they don't break down and last a long time in the environment.
Over time, companies have used these chemicals in manufacturing various products, such as firefighting foam, food packaging, and cosmetics. As a result, these chemicals have entered the air, water, soil, and food production. They discontinued the use of PFAS and their other compounds in the mid-1970s.
People believe that contamination has affected more than 7000 metric tons of Fluorochemicals. PFOAs and PFOS, which can cause various health problems, have exposed many Americans and people in the USA.
PFOA chemicals contaminated 1% of public drinking water supply systems in 2016. The EPA did not regulate safe levels of PFOA and PFOS in drinking water systems for many years.
Read More
Topics:
water quality,
advanced treatment solutions,
pH levels,
Safe drinking water,
RO system,
particulate matter,
Filter Media,
municipal water systems,
DeLoach Industries, Inc.,
Drinking Water,
Clean Water,
PFA's,
DeLoach Industries,
nylon,
Cosmetics,
reverse osmosis,
water process system,
removing PFAS & PFOS,
pfas exposure,
health effects of pfas,
exposure to pfas,
nonstick cookware,
food packaging,
water treatment standards,
PFOS,
safe drinking water act,
pfoa regulations,
the environmental protection agency,
drinking water standards,
water resistant clothing,
environmental safety,
forever chemicals