Understanding Hydrogen Sulfide Hazards and Solutions
The Science and Risks of Hydrogen Sulfide
Hydrogen sulfide (H₂S) is a colorless gas notorious for its distinctive "rotten egg" smell, detectable even at very low concentrations. This malodorous compound occurs naturally during the decomposition of organic matter and is also a byproduct of several industrial processes such as petroleum refining, sewage treatment, and paper manufacturing. With its chemical formula comprising two hydrogen atoms bonded to a sulfur atom, H₂S poses significant threats due to its toxic and corrosive characteristics.
Read More
Topics:
hydrogen sulfide (H2S),
municipal water systems,
DeLoach Industries, Inc.,
hydrogen sulfide gas,
Water Treatment Technologies
The Science Behind Hydrogen Sulfide and Its Hazards
Hydrogen sulfide (H2S) is a colorless gas known for its pungent "rotten egg" smell, even at low concentrations. With the chemical formula H2S, it consists of two hydrogen atoms bonded to a single sulfur atom. This compound is naturally produced during the decay of organic matter and can also be a byproduct of various industrial processes, such as petroleum refining, sewage treatment, and paper manufacturing. Despite its natural occurrence, hydrogen sulfide poses significant risks due to its toxic and corrosive nature.
Read More
Topics:
water treatment,
hydrogen sulfide (H2S),
municipal water systems,
DeLoach Industries, Inc.,
removing hydrogen sulfide in water,
Industrial water treatment,
scrubbers
Clean and safe water is a fundamental requirement for our well-being, yet the increasing presence of PFAS contaminants in industrial water sources remains a significant cause for alarm.
In this blog, we’ll delve into the pressing issue of PFAS contamination in industrial water supplies and shed light on how Reverse Osmosis (RO) technology is a robust safeguard against this concern. We will not only explore the effectiveness of RO in eliminating PFAS but also the distinct advantages it offers over conventional water treatment methods.
The Growing Concern of PFAS in Industrial Water
Per- and Polyfluoroalkyl Substances (PFAS) have become a growing concern in industrial water sources. Synthetic chemicals like PFOA and PFOS can stay in the environment and build up, causing significant risks to people and the ecosystem.
Read More
Topics:
water quality,
water treatment,
advanced treatment solutions,
Safe drinking water,
municipal water systems,
DeLoach Industries, Inc.,
Drinking Water,
DeLoach Industries,
removing PFAS & PFOS,
pfas exposure,
health effects of pfas,
exposure to pfas,
water treatment standards,
PFOS,
water purification systems
Water is essential for life, but not all water is safe to drink.
Contaminants like perfluorooctanoic acid (PFOA) and perfluorooctanesulfonic acid (PFOS), collectively known as PFAS, have been a growing concern in our water supply. Fortunately, there's a remarkable solution that often goes unnoticed: carbon absorption filters. Here, we'll explore the technology behind carbon absorption filters, how they effectively trap PFAS and their numerous benefits in water treatment.
Understanding Carbon Absorption Technology
Before delving into how carbon filters combat PFAS, let’s review the fundamentals of carbon absorption technology. Activated carbon, the hero in this story, is an incredibly porous material with a vast surface area, typically derived from sources like coconut shells, wood, or coal. This porous structure is what makes activated carbon ideal for trapping contaminants.
1. Activated Carbon's Structure: Think of activated carbon like a sponge, but not just any ordinary sponge – it's a super sponge! At a microscopic level, it's filled with tiny pores and holes, creating a vast and intricate network. Imagine walking through a maze with endless twists and turns – that's what the structure of activated carbon looks like. And why does this matter? Because all those nooks and crannies provide a massive surface area. It's like having a big, open field instead of a cramped room. This extra space is perfect for grabbing onto molecules, kind of like how Velcro sticks to fabric. This process is called adsorption, where molecules stick to the surface of the carbon rather than getting soaked up inside like a regular sponge.
2. Adsorption vs. Absorption: Let's clear up some confusion between two similar-sounding words. Absorption is like when a sponge soaks up water – it goes inside the sponge. But adsorption is different; it's all about what happens on the surface. Imagine you're playing with magnets. When they attract and stick together, that's like adsorption. Activated carbon is a magnet for contaminants. It doesn't suck them in like a vacuum; instead, it attracts them and sticks them onto its surface, where they stay put. So, while absorption is about taking things in, adsorption is about grabbing onto things on the outside.
3. Adsorbent Specificity: One of the remarkable features of activated carbon is its remarkable versatility and ability to adsorb a wide range of contaminants, including volatile organic compounds (VOCs), which are harmful chemicals emitted from products like paints and cleaning supplies, chlorine, commonly found in water disinfection processes, and, most importantly, PFAS, notorious for their widespread presence in water sources and resistance to degradation, making activated carbon an indispensable tool in combating environmental pollution.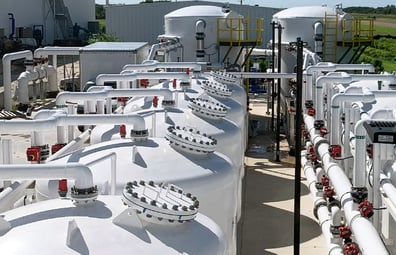
Read More
Topics:
water quality,
water treatment,
advanced treatment solutions,
Safe drinking water,
municipal water systems,
DeLoach Industries, Inc.,
Drinking Water,
DeLoach Industries,
carbon filters,
removing PFAS & PFOS,
pfas exposure,
health effects of pfas,
exposure to pfas,
water treatment standards,
PFOS,
drinking water standards,
forever chemicals,
water purification systems,
carbon absorption
In recent years, PFOA and PFOS, commonly known as "forever chemicals," have raised concerns among municipalities, food and beverage industries, and commercial facilities in the USA and around the globe. These synthetic chemicals, which never break down and pose significant health risks, have been detected in water, food supplies, and even bottled purified water. As new EPA regulations take effect in 2024, industries are searching for effective and cost-efficient methods to remove these hazardous substances from their water supply. Fortunately, advanced water purification technologies such as microfiltration, ultrafiltration, and reverse osmosis can address these challenges.
Read More
Topics:
water quality,
advanced treatment solutions,
Safe drinking water,
RO system,
municipal water systems,
DeLoach Industries, Inc.,
Drinking Water,
DeLoach Industries,
reverse osmosis,
water process system,
removing PFAS & PFOS,
pfas exposure,
health effects of pfas,
exposure to pfas,
water treatment standards,
PFOS,
safe drinking water act,
the environmental protection agency,
drinking water standards,
forever chemicals,
water purification systems,
microfiltration and ultrafiltration,
potable water,
membrane technology,
types of membranes,
flat sheet,
spirally wound
PFOA and PFOS are man-made chemicals used in various products to simplify life.
Forever chemicals, also known as synthetic chemicals called PFAS, have gained recognition. Scientists created these chemicals to make products resistant to water, stains, and sticking. The United States initially utilized them in the 1950s.
DuPont introduced Teflon in the 1950s to help Americans have nonstick cookware and make their lives easier. Americans and people from other countries liked this new improvement and soon used these substances in many different products.
These chemicals are resistant to water and lipids, so they don't break down and last a long time in the environment.
Over time, companies have used these chemicals in manufacturing various products, such as firefighting foam, food packaging, and cosmetics. As a result, these chemicals have entered the air, water, soil, and food production. They discontinued the use of PFAS and their other compounds in the mid-1970s.
People believe that contamination has affected more than 7000 metric tons of Fluorochemicals. PFOAs and PFOS, which can cause various health problems, have exposed many Americans and people in the USA.
PFOA chemicals contaminated 1% of public drinking water supply systems in 2016. The EPA did not regulate safe levels of PFOA and PFOS in drinking water systems for many years.
Read More
Topics:
water quality,
advanced treatment solutions,
pH levels,
Safe drinking water,
RO system,
particulate matter,
Filter Media,
municipal water systems,
DeLoach Industries, Inc.,
Drinking Water,
Clean Water,
PFA's,
DeLoach Industries,
nylon,
Cosmetics,
reverse osmosis,
water process system,
removing PFAS & PFOS,
pfas exposure,
health effects of pfas,
exposure to pfas,
nonstick cookware,
food packaging,
water treatment standards,
PFOS,
safe drinking water act,
pfoa regulations,
the environmental protection agency,
drinking water standards,
water resistant clothing,
environmental safety,
forever chemicals
If you’ve been reading the news lately, you know nanoparticles are not so great. In everything from cosmetics to water filters, nanoparticles have been shown to cause various health problems. But what exactly are nanoparticles, and how can you protect yourself from their harmful effects? Let’s answer these questions and more with this quick guide on removing nanoparticles from your drinking water.
Read More
Topics:
water treatment issues,
water quality,
water treatment,
advanced treatment solutions,
About DeLoach Industries,
water plant,
safety,
Safe drinking water,
Global,
distillation,
RO membrane,
RO system,
particulate matter,
filters,
municipal water systems,
residential well water systems,
DeLoach Industries, Inc.,
Drinking Water,
Clean Water,
Water Test,
Water Test Kit,
DeLoach Industries,
technology,
minerals,
temperature,
nanoparticles,
Cosmetics,
Nano,
make-up,
organ function,
contaminants,
pressure filters,
reverse osmosis,
carbon filters,
UV filters,
activated carbon
Odor control in a manufacturing facility is essential.
It prevents potential health risks and discomfort caused by the spread of chemicals, vapors, and fumes. Additionally, excessive vapors can hinder the efficiency of exhaust and natural ventilation systems.
One effective solution for addressing odor issues is the installation of an Odor Control Scrubber Tower. These towers are part of the ventilation system in manufacturing plants and chemical processing facilities.
Odor control scrubbers help to remove noxious fumes and odors from exhaust and air streams. This is an effective way to improve air quality. This process involves utilizing an activated carbon filter and an ionic air filter
Key Considerations for Installing an Odor Control Scrubber Tower:
Health and Safety of Workers:
Industrial environments pose risks of exposure to hazardous fumes and gases for workers. Unhealthy odors emitted in high concentrations can jeopardize their well-being and safety. In some cases, these gases may even be combustible, adding an extra level of danger.
Odor control scrubber towers remove gases from the contaminated air, ensuring a safe working environment. These towers reduce the risk of health issues such as nausea, headaches, allergy symptoms, eye irritation, and loss of consciousness. This helps maintain worker productivity and prevents sickness caused by toxic fumes and gases.
Read More
Topics:
water treatment issues,
water quality,
odor control,
water treatment,
water distribution system,
advanced treatment solutions,
biological scrubber,
water plant,
safety,
odor control scrubber,
hydrogen sulfide (H2S),
Chemical Odor,
caustic,
Safe drinking water,
wastewater,
gases,
Biological Odor Control Scrubber,
Biological odor control,
what is a scrubber,
municipal water systems,
DeLoach Industries, Inc.,
Clean Water,
Industrial Odor Control
Water turbidity refers to how transparent or translucent the water is when examining or testing it for any use.
Water turbidity can impact food and beverage, municipal, industrial, and aquaculture operations. Turbidity is caused by suspended or dissolved particles in the water that scatter light which causes the water to appear cloudy or even murky.
Different particles can cause turbidity, including sediments such as silts and clay, fine inorganic or organic matter, algae or soluble colored organic compounds, and microscopic organisms. Turbidity is measured in a value referred to as NTU, which means Nephelometric Turbidity Unit. The EPA requires a turbidity level no higher than 0.3 NTU in the USA, and if a member of the partnership of safe drinking water, then the level must not exceed 0.1 NTU.
High turbidity can create habitats for other harmful elements, such as bacteria or metals, that can accumulate onto the particles. This increases the health risk for a potable water system. In aquaculture operations, increased turbidity from silts and sediments can harm and harm marine life, so it must be removed to safe levels. For the food and beverage industry, the impact of high turbidity can be both a safety concern and a visual and noticeable quality concern because if the turbidity is high, it can alter the physical look of the final product, for example, a distillery.
Read More
Topics:
water treatment issues,
water quality,
degasification,
pH levels of water,
water treatment,
water distribution system,
advanced treatment solutions,
water plant,
Safe drinking water,
De-Aeration,
decarbonator,
Aqua Farming,
Fish Farming,
Aquaculture,
Pisciculture,
Deagasification,
particulate matter,
filters,
Sand filters,
municipal water systems,
industrial facilities,
DeLoach Industries, Inc.,
turbidity
Water demineralization is also called deionization and is a process known as “Ion Exchange.”
In simple terms, water demineralization is “Water Purification.” The process involves removing dissolved ionic mineral solids from a feed-water process, typically for “Industrial” water applications. Still, it can also be utilized to remove dissolved solids from a water process for “Aquaculture,” “Food and Beverage,” and the “Municipal” markets.
Why is demineralization utilized? It can remove dissolved solids to near distilled water quality at a much lower capital and operational cost than other treatment processes such as membrane softening (Reverse Osmosis). Demineralization applies the science known as “Ion Exchange,” which attracts negative and positive charged ions and allows either to attach themselves to a negative ion depending on their respective current negative or positive charge during what is known as a resin cycle. In other technical articles, we will explore and go into more specific details on the science of the ion exchange process. Water that has dissolved salts and minerals has ions, either negatively charged ions known as “Anions” or positively charged ions known as “Cations.” To treat the water and remove these contaminants, the ions in the water are attracted to counter-ions, which have a negative charge. In a demineralization treatment process, there are pressure vessels that hold resin beads which are typically made of plastic. The beads are made from a plastic material with an ionic functional group that allows them to hold and maintain an electrostatic electrical charge. Some of these resin groups are negatively charged, referred to as “Anion” resins, while others hold a positive charge and are called “Cations” resins.
There are different applications to apply Ion exchange technologies, which is why you will often hear different terminology interchanged like deionization and demineralization. The raw water quality and the specific application will dictate the type of ion exchange process needed. For example, if the water contains a high level of hardness, the water will most likely contain Ca2+ or Mg2+ dissolved solids possessing a positive charge. To replace these hard ions, it is typical to utilize a resin bed with a salt ion like Na+. As the water passes over the resin bead material within the pressure vessel. The hard ions are replaced with the salt ion; therefore, all the hardness within the water is removed. However, the water will now contain a higher concentration of sodium ions, and this must be considered during the evaluation and selection process of the type of resin material to utilize for the specific application. If the water application requires high purity and the removal of as many solids as possible, then the term or process selected is referred to as demineralization.
Read More
Topics:
water treatment issues,
water quality,
degasification,
pH levels of water,
water treatment,
water distribution system,
advanced treatment solutions,
water plant,
hydrogen sulfide (H2S),
media packing,
Decarbonation,
ION Exchange Resin,
decarbonator,
degasifier,
RO system,
H2S Degasifier,
Aquaculture,
degassed water,
Co2 ph,
removal of CO2 from water,
Deagasification,
decarbonation of water,
hydrogen ion,
particulate matter,
municipal water systems,
industrial facilities,
automated control systems,
Ion exchange,
cations,
anions